Flat Die Pelleting Machine
Let’s Start Work
Together
Please feel free to contact us. We will get back to you with 1-2 business days. Or just call us now.
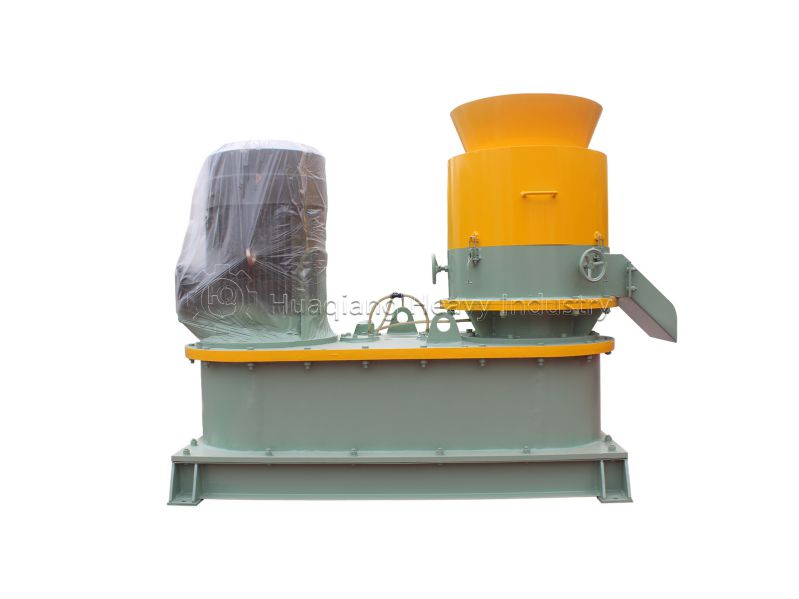
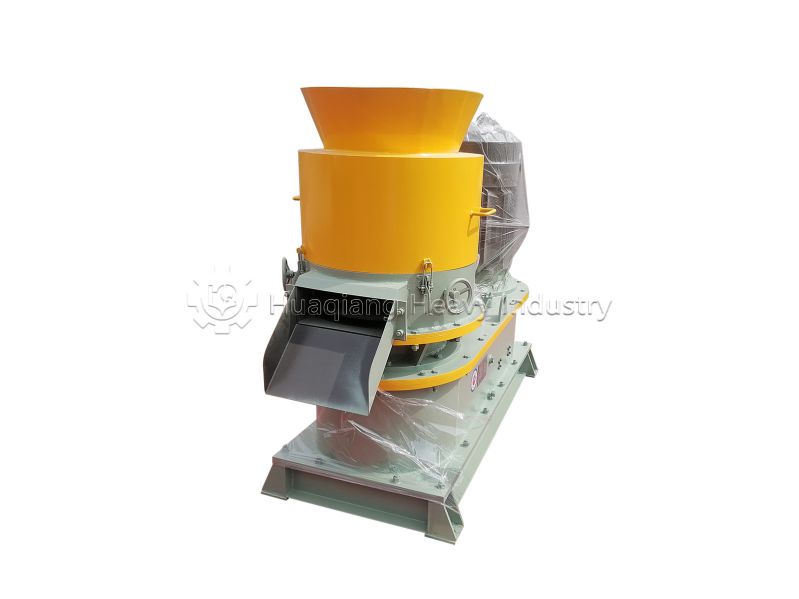
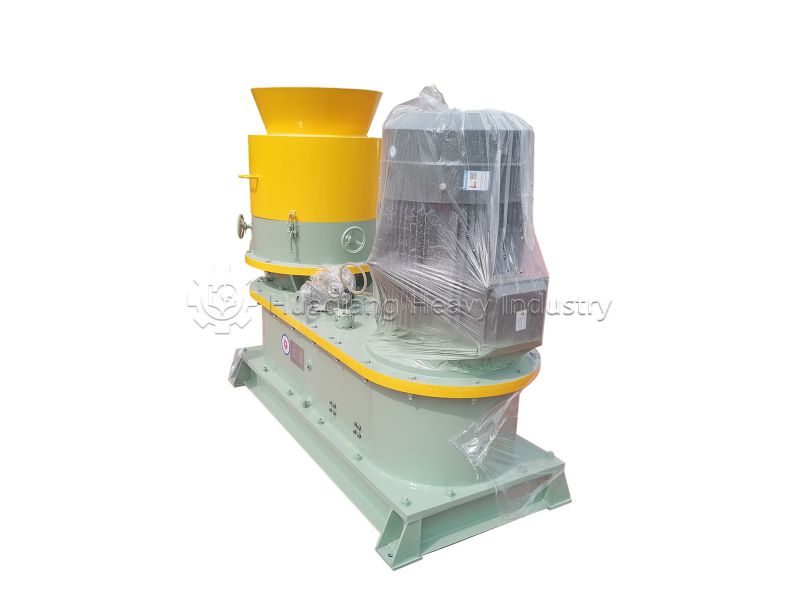
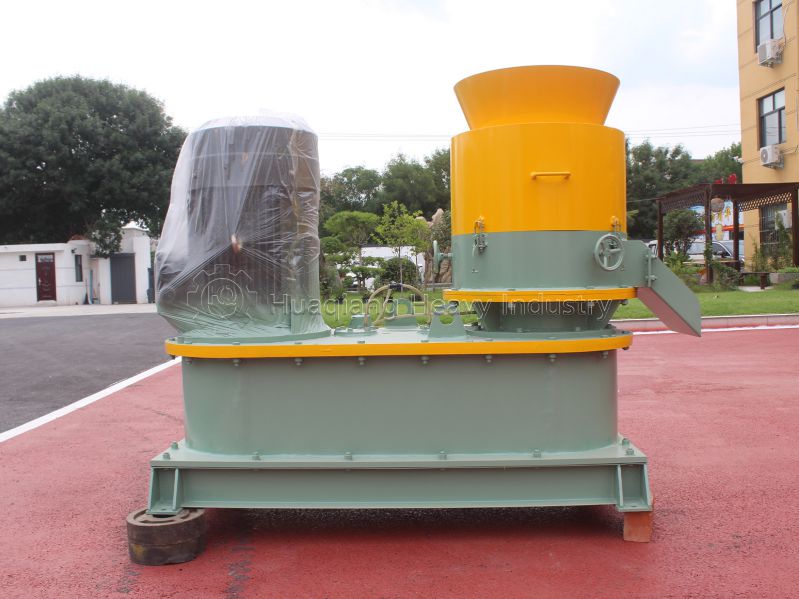
Flat Die Pelleting Machine
The flat mold granulator is suitable for granulating various materials, including but not limited to:
Biomass fuels: biomass materials such as sawdust, straw, rice husks, peanut shells, etc.
Feed industry: production of poultry, livestock, and aquatic feed.
Chemical industry: granulation of chemical raw materials such as fertilizers, catalysts, additives, etc.
Pharmaceutical industry: pre-treatment of tablet and capsule filling materials.
Scope Of Application
The flat mold granulator is suitable for granulating various materials, including but not limited to:
Biomass fuels: biomass materials such as sawdust, straw, rice husks, peanut shells, etc.
Feed industry: production of poultry, livestock, and aquatic feed.
Chemical industry: granulation of chemical raw materials such as fertilizers, catalysts, additives, etc.
Pharmaceutical industry: pre-treatment of tablet and capsule filling materials.
Equipment Structure And Composition
High pressure molding: Through high-pressure extrusion, materials that are difficult to cure can be effectively molded, resulting in good molding effects.
Wide applicability: Strong adaptability to materials, able to handle various properties of powdered or small particle materials.
Particle uniformity: By precisely controlling the pressure and mold hole size, particles with regular shapes and uniform sizes can be produced.
Continuous production: capable of achieving continuous material feed and particle output, with high production efficiency.
Moderate energy consumption: Compared to other granulation methods, flat die granulators have relatively lower energy consumption.
Compact structure: The device has a relatively simple structure, occupies a small area, and is easy to maintain and operate.
Environmental protection and energy conservation: The granulation process produces less dust and low noise, meeting environmental requirements.
Working Principle
Material preparation: Before entering the granulator, materials usually need to be pre treated, such as crushing, mixing, humidification, etc., to improve their flowability and plasticity, making them more suitable for extrusion granulation.
Material feeding: The pre treated material is evenly fed into the feed inlet of the granulator through the feeding device and enters between the flat mold and the pressure roller.
High pressure extrusion: The material is subjected to high pressure between a pair of rotating pressure rollers and a flat die. The rotation direction of the rollers is opposite, and they press the material into multiple holes on the flat mold. The shape and size of the holes on the flat mold determine the final shape and size of the particles. Under high pressure, the material is compacted and forms particles with a certain strength.
Particle demolding and cooling: The extruded particles are extruded from the flat mold holes to form a continuous strip or ring structure. These strip-shaped or ring-shaped structures are subsequently cut into particles of the desired length. In order to prevent particles from deforming or breaking during subsequent processing, there is usually a cooling process to stabilize the structure of the particles.
Post processing: The cooled particles may need to undergo screening, grading, packaging, and other post-processing processes to remove non-conforming particles and ensure the quality of the final product.
Equipment Features
High pressure molding: Through high-pressure extrusion, materials that are difficult to cure can be effectively molded, resulting in good molding effects.
Wide applicability: Strong adaptability to materials, able to handle various properties of powdered or small particle materials.
Particle uniformity: By precisely controlling the pressure and roller gap, particles with regular shapes and uniform sizes can be produced.
Continuous production: capable of achieving continuous material feed and particle output, with high production efficiency.
Low energy consumption: Compared to other granulation methods, the energy consumption of the roller extrusion granulator is relatively low.
Compact structure: The device has a relatively simple structure, occupies a small area, and is easy to maintain and operate.
Environmental protection and energy conservation: The granulation process produces less dust and low noise, meeting environmental requirements.